In many industrial productions fiber composites are of growing interest and used in ever more diverse setups. For example in aircraft and wind power plant construction carbon reinforced fiber composites are nowadays of utmost importance. These high-performance materials are very costly. Hence, for safety and especially from an economic point of view, it is important to detect damages as soon as possible before greater parts of a structure deteriorate.
Traditional materials such as steel change slowly from an elastic to plastic deformation. Fiber composites however behave very differently. Small delaminations of single layers or growth of fissures can barely be seen by naked eye but might lead to severe damages or failure of the structure. Hence, the development of robust and reliable Structural Health Monitoring (SHM) systems are important to enhance safety and to decrease maintenance intervals and, lust but not least, costs at the same time. A SHM system consists of a network of piezo-ceramic sensors and actuators that are attached to the structure’s surface (see sketch below). The sensors then measure signals that come from the actuators, travel through the entire structure and interact with possible defects.
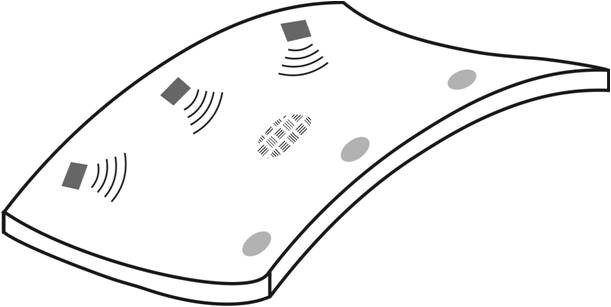
The mathematical model of wave propagation in elastic structures is given by Cauchy’s equation of motion which is, depending on the applied constitutive law, a linear or nonlinear hyperbolic system of PDEs with initial and boundary values. A SHM system has to solve the inverse problem of computing parameters of the PDE, such as, e.g., the modulus of elasticity or the stored strain energy function, from sensor data that are acquired at the surface. Because of its nonlinearity, time-dependency and high dimensionality this inverse problem is amongst the most challenging tasks in this area. A reconstruction of a damage based on the Landweber iteration can be seen in the figure below, where the yellow dots mark the sensor positions.
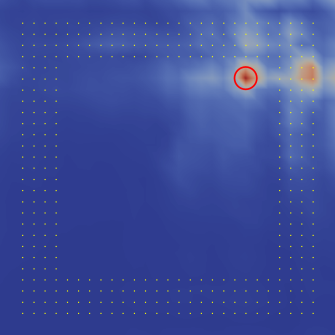